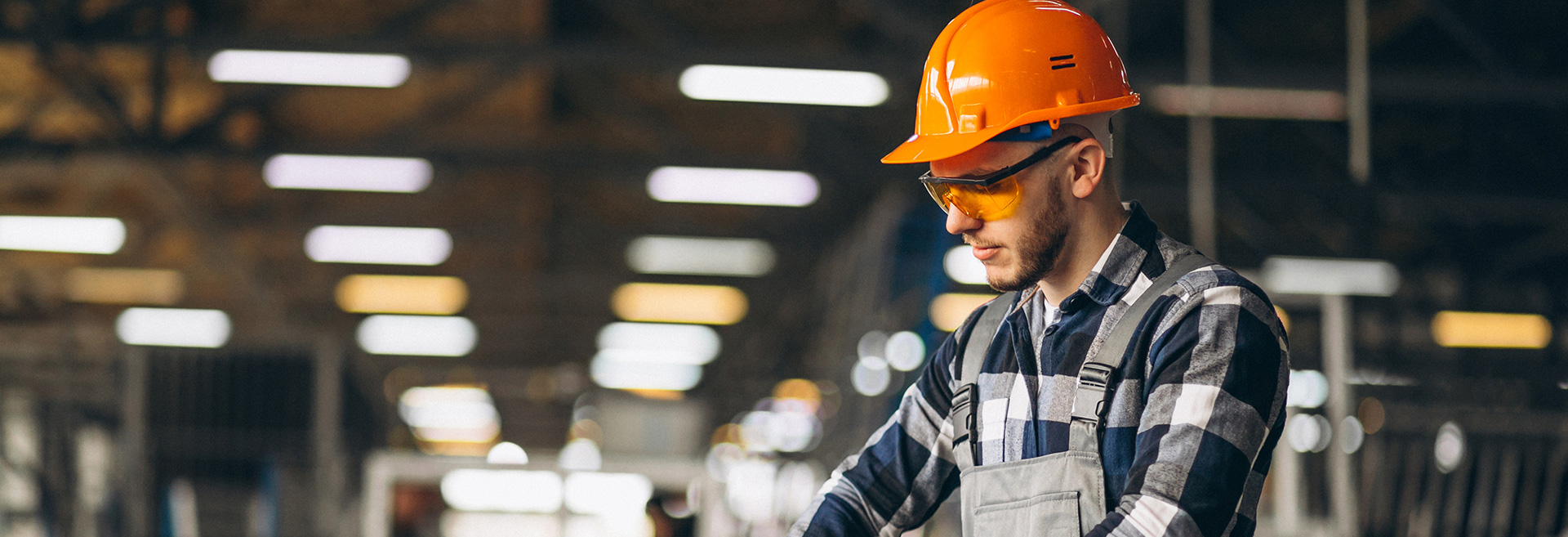
Aerospace
Aerospace
Lightweight design is an extensively explored and utilized concept in many industries, especially in aerospace applications. The principle of lightweight design is to use less material with lower density while ensuring the same or enhanced technical performance. A typical approach to achieve lightweight design for aerospace components is to apply advanced lightweight materials or composites to replace metal components. Metals have the advantages of ease of manufacture, but composite materials are particularly attractive to aviation and aerospace applications because of their exceptional strength- and stiffness-to-density ratios and superior physical properties.
Composite manufacturing processes, such as vacuum bagging, require high temperatures for chemical reactions which result in sticky situations. We offer the perfect processing solutions for your composite manufacture with our extensive line of chemically inert, anti-adherent and high temperature processing aids.
The aerospace industry relies heavily on high-performance fluoropolymers, which are used in a wide range of temperatures while maintaining performance, and can also offer chemical resistance when exposed to corrosive fuels. Fluoropolymers are widely used in the aerospace industry because they are much lighter than other aerospace building materials that offer agility, increased speed to the aircraft and reduce fuel consumption. HiTemp offers a variety of fluoropolymers like FEP, ETFE, ECTFE, PFA in varied thickness & roll lengths that provide excellent qualities like high-temperature use, chemical inertness, wear resistance and non-leaching properties.
features-and-benefits
Features | Benefits |
---|---|
Low Surface Energy | Excellent release and self-cleaning capabilities |
Functional temperature range from -200°C (-328°F) to 165°C (330°F) | |
Highest Dielectric Strength | Excellent insulator in many applications |
Non-Flammable | Meets safety requirements for aviation and military applications |
Highest mechanical strength in fluoropolymer film | Allows greater design flexibility over other fluoropolymers |
Lower density than ETFE and FEP | Lighter weight constructions for high performance applications |
Highest Abrasion resistance | Suitable for tough indoor and outdoor environments |
CHEMFILM® PFA-PG Fluoropolymer Film Typical Properties*
Typical Properties | Test Method | Value | Units |
---|---|---|---|
General | |||
Specific Gravity | ASTM D-792 | 1.68 | |
Yield | 22(115) | m2/kg (ft2/lb) | |
Water Absorption, 24 hr. | <0.01 | % | |
Mechanical | |||
Tensile Strength | ASTM D-882 | 55(8000) | MPa (psi) |
Elongation, Ultimate | ASTM D-882 | 250 | % |
Tensile Modulus | ASTM D-882 | 1375(200000) | MPa (psi) |
Initial Tear Strength | ASTM D-1004 | 4.4(450) | N(gm/mil) |
Propagation Tear Strength, 1 mil | ASTM D-1922 | 11.6(1200) | N(gm/mil) |
Fold Endurance (M.I.T) | ASTM D-2176 | >250000 | cycles |
Electrical | |||
Dielectric Strength, 1 mil | ASTM D-149 | 216(5500) | kV/mm (V/mil) |
Dielectric Constant, 1 kHz | ASTM D-150 | 2.55-2.63 | |
Dissipation Factor, 1 kHz | ASTM D-150 | <0.005 | |
Thermal | |||
Melt Point | ASTM D-3418 | 240(465) | °C (°F) |
Continuous Service Temperature | 300-340 | °C (°F) | |
Flammability | ASTM UL-94 | V-0 | |
Heat Sealing Temperature | 245-260(475-500) | °C (°F) |
Related Documents
Application
- I. Vacuum Bagging
Vacuum bagging is a manufacturing process that makes composite parts with the use of a mold with the form of the part and with the use of several layers that create mechanical pressure on the laminate during its cure cycle. These molds can be brought into an autoclave oven where the parts cure under the pressure. Flexible release films, fabrics and tapes are part of the layers that allow the part to release from the mold upon cure, while applying the pressure during the cure. HiTemp line of fluoropolymer films, fabrics and tapes, withstand the temperatures, and have the chemical inertness and release properties required for the process.
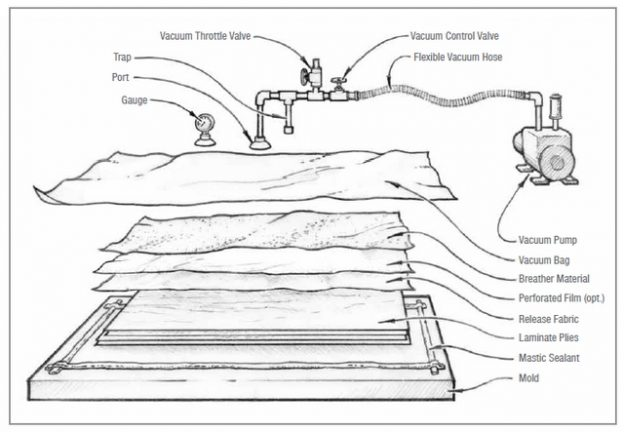
- HiTemp HiFilm FEP 1 Mil Red
- HiTemp HiFilm FEP 2 Mil Red
- HiTemp HiFilm ETFE 1 Mil Blue